The company used an artificial intelligence algorithm to try to come up with new concrete recipes that release less carbon dioxide.
Author: Steven Strong
Why The Concrete in Public Works Projects Lasts for Generations but Your Driveway Doesn’t
A ‘Greener’ Cement Supporting Sustainability and Reducing Carbon Footprint
Filiberto Ruiz
President and Chief Executive Officer, Votorantim Cimentos North America
Vice Chairman, PCA Board of Directors
Concrete is ubiquitous in our daily lives. As the world’s most-used man-made material, it is an essential part of infrastructure improvements and new construction throughout North America. Concrete is durable; resilient; doesn’t rust, rot, or burn; and can withstand powerful storms. Now, it is also greener.
Portland-limestone cement (PLC) is a type of cement that has been common internationally for decades but is still relatively new to North America. PLC’s main benefit is a lower carbon footprint, with CO2 emissions reduced during production by 10% on average. In fact, by shifting production to PLC, manufacturers have already reduced CO2 emissions by more than 325,000 metric tons in the U.S. from 2012-2018 — equivalent to the amount of CO2 stored in over 400,000 acres of forest — without sacrificing the material’s physical properties needed for their projects.
Here are a few examples how PLC is already helping reduce CO2 emissions in the U.S.:
- Using PLC contributed to a 50% lower carbon footprint for Mississippi State University’s Davis Wade Stadium.
- Using PLC to build new bridge decks, the Tennessee Department of Transportation saved about 50 lbs. of CO2 for each cubic yard of concrete – the equivalent of the energy emissions from charging 2,892 smartphones.
- Using PLC to construct the University of California, San Diego biomedical research facility resulted in a 160-ton reduction in CO2 emissions, which is equal to the energy emissions from burning 176,298 lbs of coal.
- The ongoing construction of the Drexel University Academic Tower is using PLC and saving about 370 tons of CO2 emissions – equivalent to energy emissions from 41,634 gallons of gasoline consumed.
These examples prove that as we continue to rely on concrete to support our thriving cities and rural areas, the cement and concrete industry is working diligently to ensure the building materials we need are becoming more sustainable. Because of the scale at which concrete is used, even small changes to its formulation to make it greener can have a dramatic positive impact on emissions.
PLC is produced in a way that is very similar to traditional portland cement, the only difference being more limestone is used during the mixing process, resulting in a reduction in CO2 intensity.
PLC has undergone extensive testing and research in the United States and other countries to ensure its durability and resiliency. Builders and designers can expect the same strength with minimal disruption and change to their projects. The decrease in CO2 emissions makes PLC a more sustainable, yet equally resilient and dependable option as a building material.
The cement and concrete industry is committed to continuing research and innovation to provide greener solutions to improve upon these essential materials, helping to create more sustainable communities and an environmentally responsible future for our planet.
To learn more specifics about portland-limestone cement, visit greenercement.com. And, to Learn more about the cement and concrete industry’s commitment to sustainability visit shapedbyconcrete.com.
Reducing Carbon Footprint with PLC
A new ‘greener’ cement supports sustainability efforts
Concrete is ubiquitous in our daily lives and a key part of building sustainable, resilient communities. The cement and concrete industry is committed to research and innovation to evolve and provide solutions to continue to improve upon these essential materials, helping to create a more environmentally responsible future.
Portland-limestone cement (PLC) is a type of cement that has been common internationally for decades but is relatively new to North America. PLC’s main benefit is a lower carbon footprint, reducing carbon dioxide emissions during production by 10% on average. In fact, by shifting production to PLC, manufacturers have already reduced carbon dioxide emissions by more than 325,000 metric tons in the U.S. from 2012-2018, equivalent to carbon stored in over 400,000 acres of forest.
Concrete is the most used building material in the world and a key part of U.S. infrastructure because it is durable; resilient; does not rust, rot or burn; and can withstand powerful storms. Now, it is also greener.
What are the benefits?
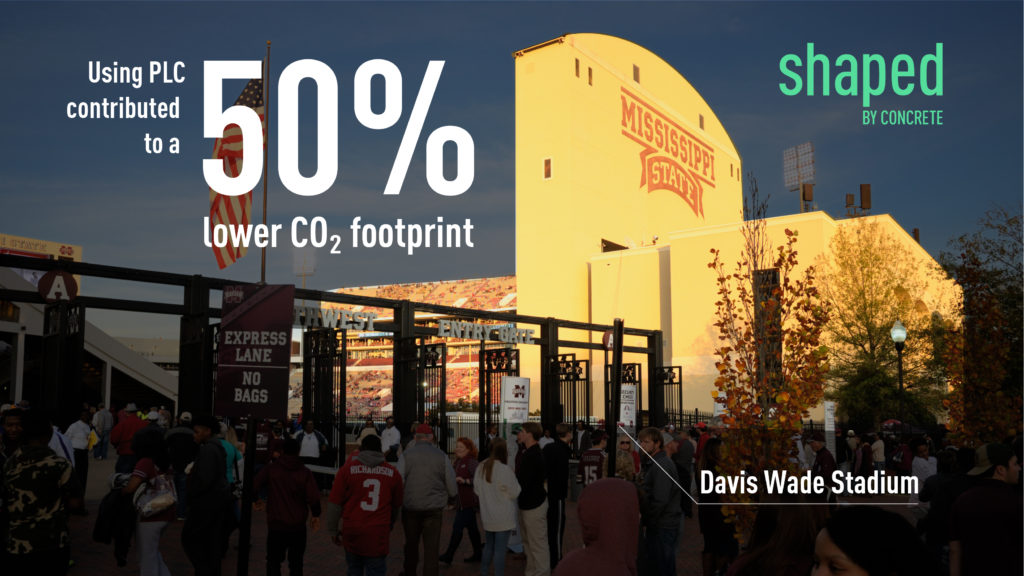
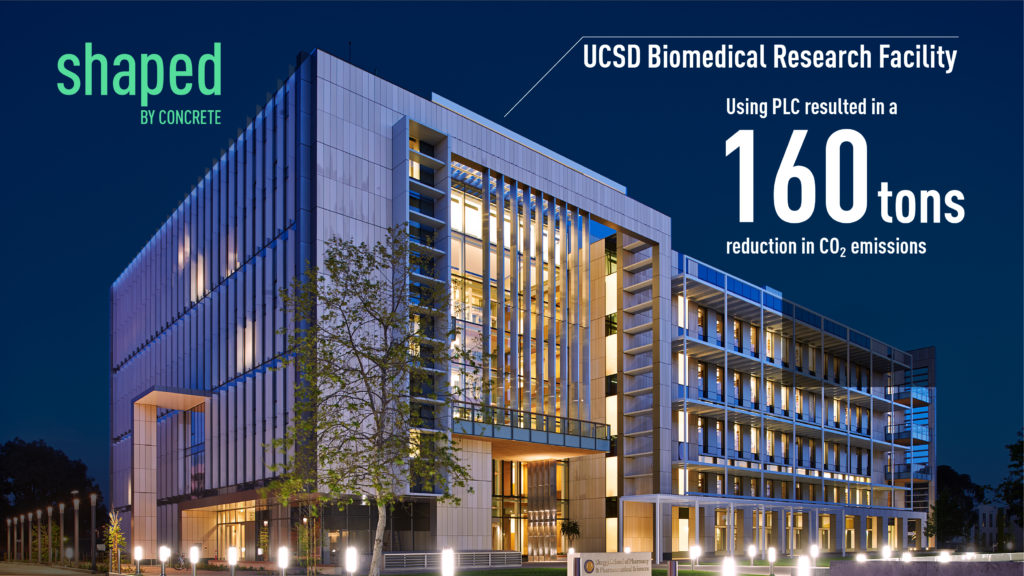
How does it work?
PLC is produced in a way that is very similar to traditional portland cement, the only difference being more limestone is used during the mixing process, resulting in a reduction in carbon dioxide intensity.
PLC has undergone extensive testing and research in the U.S. and other countries to ensure its durability and resiliency. PLC also is simple to switch to as it is a 1:1 replacement for traditional portland cement. This allows users to continue their standard operations with minimal disruption and change. The decrease in carbon emissions makes PLC a more sustainable, yet equally resilient and dependable option as a building material.
As we continue to rely on concrete to support our thriving cities, the cement and concrete industry is ensuring that the second most used materials in the world continues to evolve and become more sustainable. Because of the frequency that concrete is used, even small changes to its formulation, making it greener, can have a dramatic impact on emissions.
To learn more about PLC, visit greenercement.com.
For more information about the sustainability properties of concrete, visit Sustainability Practices in the Cement and Concrete Industry.
For more information about the impact of cement and concrete across their full lifecycle, visit Concrete Creates Sustainable and Environmentally Responsible Infrastructure.
The Most Sustainable Building is One That Only Needs to be Built Once
Ron Henley
President – GCC of America
Portland Cement Association (PCA) Chairman of the Board
Concrete is a key part of building a resilient future, providing unparalleled durability, strength, and security. Not only is concrete better able to withstand normal wear and tear, but it also enhances the ability of our communities to withstand natural disasters worsened by climate change by reducing the risk of significant damage; protecting us against high winds, fires, and storm surges; and lowering the time and costs needed to rebuild communities.
When it comes to resiliency – which is measured by whether building occupants can safely shelter during natural disasters and whether the structure itself can survive – concrete is the most resilient building material. If a structure can be repaired rather than replaced following a disaster, it is faster, less expensive and more energy efficient return to normalcy for cities, residents, and business operations.
Increased durability from concrete provides economic benefits, especially in disaster-prone areas: every $1 spent on resilient building and construction can save $6 in recovery costs according to a recent study by the National Institute of Building Sciences. Furthermore, the National Oceanic and Atmospheric Administration forecasts predict more storms and major hurricanes than average this year. Considering that from 2015-2019 there have been at least 10 disaster events each causing over $1 billion in damage, savings from resilient concrete construction can quickly scale up.
Since the expected cost of maintenance and post-disaster repairs can exceed initial building costs, the economic case for resilient construction using concrete is simple: a small investment up front pays exponential dividends throughout the life of a building. Even with those benefits, studies have shown concrete to be cost competitive to other building materials at every level of resilience.
Builders, architects, and designers have come to recognize that buildings and homes built with concrete are more durable and resistant damage from natural disasters. Resilient structures also benefit our planet because their environmental footprint can be spread over several decades. Concrete truly offers the best mix of safety, resiliency, affordability, and sustainability.
As the most widely used construction material, concrete is readily available, cost competitive with steel and wood, and resilient. And it will continue to have a key place in creating a resilient – and sustainable – future.
If you would like to learn more about the resiliency of concrete or our campaign, please visit Shaped by Concrete
Bendable Concrete and Other CO2-Infused Cement Mixes Could Dramatically Cut Global Emissions
How We Will Get to Carbon Neutral Concrete By 2050
Michael Ireland
President and CEO at Portland Cement Association
The cement and concrete industry is taking significant steps toward addressing climate change and emissions. Late last year, the Portland Cement Association announced plans to develop a roadmap for its member companies to achieve carbon neutrality across the concrete value chain by 2050.
To reach this goal, it is imperative that we have partnership from stakeholders along the concrete value chain; we cannot address this problem alone. Only by working together as an industry can we hope to realize the multitude of solutions that must be developed across policies and regulations, technology and innovation and demand generation.
The United States industry aligning under a formal and measurable commitment to reduce emissions comes at a critical time in our country. As the U.S. transitions into a Biden administration, our industry is optimistic about the potential of environmental progress being made in a bipartisan manner. We are hopeful for the opportunity to further collaborate with federal officials and work together to achieve our shared climate goals.
Additionally, the economic and health crisis brought on by COVID-19 represents an opportunity to build back better. Responsible leadership in the manufacturing and use of cement and concrete will be a critical part of creating a more sustainable built environment and future. After all, cement and concrete are the foundation of our homes, connect our communities, encourage trade and enable prosperity.
The cement and concrete industry will be a leading voice in enabling the construction sector to rise and meet this challenge. With the formation of PCA’s new Sustainability Council, comprised of sustainability experts from our members companies, and with input from external experts, we will develop the roadmap that will guide us on perhaps the most ambitious decarbonization journey ever attempted.
Cement manufacturers have a history of innovation and modernization. Cement and concrete was one of the first industries to address climate issues in the mid-1990’s reducing energy consumption by more than 35% while actually increasing production. Investing in new innovative technologies and working with academic partners like the MIT Concrete Sustainability Hub will be key to ongoing research efforts. The roadmap will also explore how to stimulate demand for low-carbon materials, from building awareness to educating architects and developers on the latest sustainable options. We are proud to accelerate those efforts even further by developing this roadmap toward carbon neutrality.
We are committed to addressing climate change and supporting a sustainable circular economy, and this roadmap will enable PCA’s member companies to continue building a better future.
Concrete Creates Sustainable and Environmentally Responsible Infrastructure
Looking at the full lifecycle of infrastructure, concrete and cement enhance sustainability
QUICK FACTS
- Concrete structures have similar amounts of embodied carbon dioxide and energy when compared to other building materials. Embodied carbon dioxide is the carbon dioxide associated with building construction, including extracting, transporting and manufacturing materials.
- Concrete is the most durable, resilient building material due to its long service-life and ability to withstand the elements, and it requires less maintenance and repairs, meaning less energy and emissions for upkeep compared to other building materials.
- Concrete actually absorbs carbon dioxide over its entire life and captures it permanently, but unlike other sources which may also absorb carbon dioxide, such as wood, it will not rot and release that carbon dioxide back into the environment.
Concrete made with cement is the most used man-made product in the world. As climate concerns grow, these foundational materials are uniquely positioned to help us meet the challenges of a more sustainable world.
Carbon dioxide emissions from all sources, including the building sector, are receiving increased attention. While the cement industry was one of the first to acknowledge climate change issues and implement tangible steps to reduce emissions through programs focused on process and energy efficiency, the major sustainability benefits of concrete made with cement are not widely known.
Concrete and cement play an important role in our economy and are an essential part of a sustainable future.
We need to take a lifecycle approach
In order to truly determine which building materials are the most sustainable, we must consider them in terms of their entire lifecycle, that is, from sourcing and production through end use and disposal. Specifically, for building materials such as concrete, wood, steel and glass, the best way to measure environmental impact is by looking at their embodied carbon and energy.
Embodied carbon is all the carbon dioxide emitted and energy expended during the sourcing, manufacture, transport, construction use, reuse, recycling and disposal of building materials.
Why a lifecycle approach?
Looking at just one stage of a material’s service life is not an accurate measure of how much carbon dioxide or energy is expended in relation to that material and it is misleading when we think about solving a complex challenge such as climate change.
Although cement’s carbon footprint for production is higher than some other materials, concrete itself has a low carbon footprint. In fact, concrete has similar embodied carbon (e.g., carbon per kilogram of concrete) to most common building materials, but its impact appears much greater because we use so much of it – it’s the second most consumed material on Earth after water. Concrete’s global prevalence is for good reason – it is available, durable, versatile and cost-effective. It is also sustainable, playing a part in limiting or reducing building emissions and being 100% recyclable.
A lifecycle assessment of several building types conducted by MIT has shown that embodied environmental impacts of buildings are around 10% of the total lifecycle greenhouse gas emissions; energy use (such as heating, cooling and maintenance of the building) represents the vast majority of environmental impacts. Simply put, the impact of creating a building is just a small part of the picture, compared to the energy and emissions required to operate the building over its life.
Production (the 10%)
Cement and concrete production is heavily regulated and monitored, with standards in place for each step in the manufacturing process to measure and understand environmental impact. But production within other building material industries is not always monitored in the same way. Often the energy and emissions associated with sourcing materials and transportation, such as in the timber industry, is not considered when measuring embodied carbon.1
In addition, cement and concrete production offers opportunities for innovation and increased efficiency. As part of their ongoing work to lower emissions, many cement manufacturers have recently introduced a type of cement called portland-limestone cement in the U.S., which lowers carbon dioxide emissions about 10% during production. Many have also incorporated alternative fuels like biomass and waste materials into production, which are less carbon intensive and result in lower emissions. Additionally, promising innovations such as carbon capture and storage technology are being evaluated which can help cement plants reduce their overall carbon footprint.
Construction and use (the other 90%)
The most sustainable building is one that you only have to build once and can maintain efficiently. Durability and resilience are vital parts of sustainable construction, as insufficient durability or resilience may result in a reduced building life, unexpected repairs or even total reconstruction, with all their associated costs and social impacts. Concrete structures typically have a longer service life than ones made with steel and timber, as they do not rust or rot and are pest resistant. Moreover, concrete structures can be repurposed avoiding having to destroy and reconstruct buildings using new materials which would create pollution and use more energy.
Use
Over the course of a concrete building’s lifecycle, concrete is continually absorbing and trapping carbon dioxide from the air and offsets more than 11% of the carbon dioxide emitted to produce it. Importantly, concrete will not burn, rust, rot, or re-release that carbon dioxide back into the environment.
Wood, the only other construction material that can sequester carbon dioxide, captures carbon dioxide while the tree is alive and will emit that carbon dioxide if it rots or burns.
Cement and concrete building materials also exhibit excellent thermal insulating mass, improving the energy efficiency of buildings. Studies by MIT have shown that homes with concrete walls can use 8 to 15% less energy than other homes.2
End of Life
Concrete’s unparalleled durability enables buildings to be reused and repurposed, extending the lifespan of construction and reducing waste over time. Additionally, concrete is 100% recyclable – structures built from concrete can be crushed and recycled for other functions without material loss or pollution. Every exposed concrete surface absorbs carbon dioxide and deconstructing a concrete building and crushing the concrete into pieces offers the potential for greater carbon dioxide uptake.
When determining which building materials to use for our infrastructure, we must look at the entire life cycle of the structure (building, road, bridge) to understand how the materials it’s made from impact its use phase. Only then can we make informed decisions to move us closer to our sustainable development and emissions reductions goals.
For more information about the full lifecycle impact of cement and concrete, visit Cement and Concrete Lifecycle.